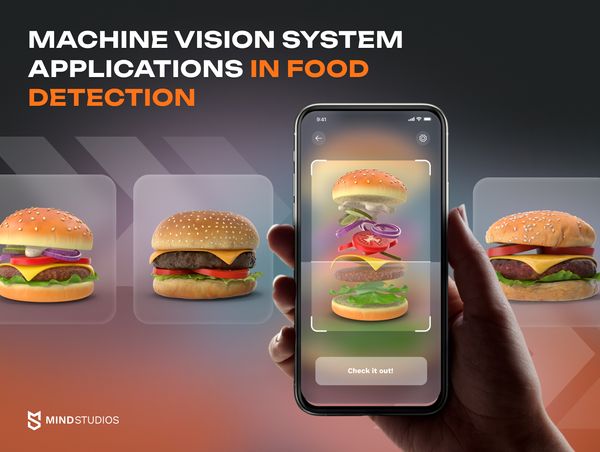
As one of the most current artificial intelligence technologies, artificial vision has been developed to give industrial equipment the capacity to perceive, analyze, and manage production, quality control, and asset safety duties. Because of its numerous advantages, it has become an important component of today's most in-demand systems.
The development of automated machinery has greatly improved the efficiency and productivity of the food processing sector. Manufacturers of food items are increasingly turning to automation to meet rising consumer demand while also improving efficiency, cutting costs, and maintaining high quality and safety requirements.
At the same time, machine vision has been around for quite a while now — devices employing the predecessor tech of what we have today were used in some production facilities since the 1950s, though it wasn't until the 1980s and 1990s that they truly took off. And now, it is an integral part of modern industry.
It is a current technology utilized by many businesses, particularly those in the industrial sector. However, machine vision systems are ineffective without a solid software foundation. Hence, it is critical to devote the same amount of time and resources to the system's software as one would to its hardware.
This article will describe what this intelligent implementation implies and how Mind Studios can help you create that software foundation and ultimately help your company become a part of a digitalized future.
Understanding machine vision and its applications
Machine vision systems are usually defined as "technology that allows a computing device to inspect, evaluate, and identify still or moving images." One of the most basic ways to understand a machine vision system is to think of it as the "eyes" of the machine. The system determines action based on digital input acquired by a camera. Machine vision systems are used by businesses to improve quality, efficiency, and operations in many ways.
When employed in manufacturing, a machine vision system consists of an array of electrical components, computer hardware, and software that work together to interpret and analyze collected pictures for operational guidance. The following are the typical components:
- Sensors
- Frame-grabber
- Digital and analog cameras
- Sufficient lighting for cameras to capture high-quality imagery
- Images that can be analyzed using software and computers
- Pattern recognition algorithms (useful in multiple fields)
- Output devices like a screen or a set of mechanical components
To mention a few applications, the technology and techniques may be utilized to discover faults, offer product sorting, barcode scanning, end-of-line vehicle inspection, product checking, and robotic manufacturing.
Machine vision can also be a powerful image-processing tool, allowing for the recognition and classification of objects, patterns, and other data. Stitching, filtering, thresholding, pixel counting, segmentation, edge detection, color analysis, and blob identification are all steps in this procedure. Deep learning and machine learning processing have greatly expanded machine vision capabilities, yielding classification, pattern recognition, barcode scanning, optical character recognition, and measuring methodology. Machine vision systems can usually measure things like:
- Pass or fail decisions
- Object position and orientation information
- Numerical measurement data
- Data read from codes and characters
- Object counts (like paper boxes, bottles or other forms of packaging) and classification
- Process or result displays which are stored for later use
Deep learning has enabled the creation of image-based robot guidance, which provides location and orientation information to let robots grip products and move.
Even though machine vision was created first, the technique should not be confused with computer vision. This concept is based on how computers may be programmed to learn from digital pictures or video feeds and automate a human visual system. This can be confusing since many of the same methods and concepts are used in computer vision, however, the limitations and applications are different.
Software for machine vision system
When processing an image, computer vision software often performs multiple steps. The majority of machine vision software first alters the image to remove noise or convert several shades of gray to a basic black-and-white combination. After first simplifying the image, the program will count, measure, and/or detect items, size, flaws, or other aspects in it. The following are the most frequently used elements of computer vision system software:
- Image processing: An essential component of any machine vision system for it to function properly.
- Contour analysis: Extremely beneficial in agricultural and food production.
- Shape fitting: Critical in conveyor manufacturing.
- Camera calibration: Guarantees that all visual sensors are properly configured throughout production.
- Barcode reading: An important piece of software for proving the quality of manufactured items.
- 1D and 2D Measurements: The purpose of 1D software is to identify and categorize faults in products made in a continuous process, such as paper, metal, plastic, and non-woven packaging. 2D software tools assist in the creation of area scans that are suitable for individual elements.
- Template matching: A high-level computer vision software feature that finds picture components that fit a predetermined template.
- Deep learning: This feature can successfully recognize the type and quality of food when paired with calibrated image processing tools.
Finally, when combined, the software passes or fails the part based on predetermined criteria. If one part of the process fails, the computer vision tool may instruct a mechanical device to reject it, or the computer vision program may stop the manufacturing line and notify a human worker about the problem.
Applications of machine vision systems in food detection
Various detection and measurement technologies are used in current food automation production: foreign item detection in mineral water, print quality inspection of beverage bottle caps, and barcode and character identification on product packaging. These applications have the trait of continual large-scale manufacturing with extremely high criteria for aesthetic quality.
Due to this, such tasks (and they are highly repetitious) are usually entrusted to humans for manual examination.
In certain industries, we frequently witness hundreds or even thousands of inspection personnel working behind enhanced manufacturing lines. This not only increases the factory's staff and management expenses but also makes it impossible to ensure a 100% inspection certification rate with zero errors.
In today's cutthroat business climate, not even a 0.1% inaccuracy is accepted. Defect detection is required to assure product quality throughout production. Human eyes cannot always do the job in a consistent, stable, and efficient manner, especially when it comes to small-size precise and rapid measuring, shape matching, and character coding. As a result, machine vision inspection technology is introduced due to its speed, dependability, and reproducibility of results. The advent of machine vision measuring has significantly compensated for this flaw.
Machine vision systems have several uses, particularly in the food, beverage, and food processing sectors. Below, we take a closer look at how machine vision can be employed.
Package verification and labeling
Labelling and information printing are the most detail-oriented aspects of packaging, and this is where the food production business suffers the most. Not only does a lot of expensive design material go down the sink due to a little printing error, but also a lot of manufacturing money is squandered. Needless to say, the brand image is harmed when an item has an incorrect packing size or has initials printed on it. Adapting machine vision solutions, which can quickly carry out important packaging qualities through increased categorization, optical character recognition (OCR), and detection algorithms, will be the final answer to these harmful blunders in the future.
Beverage production
Because of high-speed manufacturing and packing lines, the food sector has undergone substantial changes, making it more difficult to ensure the items delivered to consumers are of high quality.
Manufacturers confront obstacles by recognizing and addressing defects in their products, as well as ensuring proper product filling. Machine vision is critical in improving the manufacturing quality of beverages and conveyor performance by assuring assembly, tracking, packaging, labeling, and gathering critical data at each stage of the process.
Manufacturers can now calibrate high-end automated machinery for a variety of inspections in beverage production, such as case completeness, bottle type verification, sticker verification, cork inspection, QR code inspection, bottle inspection, fill-level inspection, cap seal inspection, and more.
If you would like to know how to create a food delivery website from scratch you can learn about the whole process in our article.
Product sorting and quality control
One of the major challenges facing the food sector is achieving the highest possible standard of quality control in 100% of production. To do this, all visual parameters of the product must be controlled at various stages of production. This includes metrology parameters (2D and 3D), vision analysis of measurable parameters, and artificial intelligence analysis of non-measurable parameters. Likewise, there are numerous difficulties in identifying and correctly classifying the items, which can be due to a variety of factors, including:
- Natural and handmade products that are distinctive in every way
- Metrology control of multiple variables based on product type
- Control of subjective characteristics such as toasting degree
The quality control system is capable of the following tasks:
- Product identification on the production line
- Performing different tests on each product based on its type
- Product classification based on various visual criteria utilizing artificial intelligence, i.e. deep learning
Here's a use case in meat production. Inndeo, a Spanish company, utilized hyperspectral scanners along with a machine vision system to make it possible to look at produce at a completely different angle. A custom-built system like this can analyze up to 200 items each minute, 24 hours a day. Non-conforming items are automatically sorted out. At the same time, almost no upkeep is necessary.
In addition, a program like this conducts 2D and 3D metrology, as well as deep-learning-based segmentation and classification. As a result, the segmented produce pieces are categorized (using classic machine vision algorithms and applications) based on their visual appearance. This would not have been possible or would have required a significant amount of programming effort without the integrated deep-learning functions. Below are the main benefits of using machine vision for quality control:
- All quality variables are under control
- Production capacities that have been released can now be used elsewhere
- Increase in output
- Up to 100% of production can be analyzed
- Standardization controls that could not previously be carried out are applied
Fruit sorting and defective fruit grading
Traditional machine vision solutions could only identify between basic fruit forms and sizes and could not assess the color, root, and stem quality of the fruit.
In a study published by the College of Engineering of China Agriculture University color sorting was used to determine defective fruits. By using color sorting, the system captures photos of the fruit from various angles using high-resolution cameras and advanced lighting algorithms.
The system employs edge detection algorithms to quantify even the smallest root and stem in root and stem sorting, allowing it to properly analyze the quality and condition of the root and stem. This improves sorting accuracy and enables the discovery of concealed flaws that previous machine vision systems in the food industry would have overlooked.
Shelf life assessment and freshness monitoring
Fresh items may be kept for a long period, however, decaying goods must be sold quickly. Similar grading techniques may also be used to determine the worth of objects.
To guarantee that customers always receive the freshest possible food options, computer vision may be used effectively for freshness detection.
Freshness grading of vegetables and fruits manually is a Herculean undertaking. Because there is no defined vegetable freshness categorization system, we must physically inspect each item while purchasing fresh fruits and vegetables from the supermarket. When we go to buy in huge quantities, it takes a long time and the product quality is not guaranteed to be good.
Luckily, recent advancements in computer hardware and artificial intelligence approaches have created new opportunities in a variety of industries, including agriculture.
A multiple non-linear regression (MNLR) model connecting temperature and maximum shelf life was proposed in a study conducted by the Polytechnic University of Cartagena to tackle daily deterioration and degradation. This model predicts when items will lose their theoretical shelf-life in case of inappropriate temperature settings during storage or transit. The technology, which was created as a sensor-based tool, has been tested on various ground transportation journeys around Europe.
It is important for food to be delivered on time. If you want to come up with your own delivery app, let Mind Studios help your idea come to fruition by contacting our experts today.
Use cases and examples of machine vision technology applications
As you may have noticed, there is a wide range of machine vision applications in the food business. However, incorporating a machine-based system into a company model may be a costly venture, and you never know if the investment is worthwhile, especially if you operate a small business. We examined the most prevalent use cases that assisted medium-sized firms in not only implementing machine vision in their day-to-day operations but also profiting from it.
Food sorting: application of machine vision system in optical sorting solutions
Previously, companies had to recruit many people to undertake the boring and regular tasks associated with food selection. Instead of manually sorting vast volumes of food by size and shape (so that it may be canned, bottled, or bagged), AI-based software solutions can now readily distinguish which plants should be used for potato chips and which should be used for french fries instead.
The same technology will pick out vegetables of an unsuitable hue, reducing the likelihood that they will be abandoned by purchasers. Recently, TOMRA Food Sorters and Peelers improved processing capacity and availability, resulting in higher food quality and safety. This was accomplished via the use of core sensor technologies, tailor-made software, and a camera that detects material based on color, biological properties, and form (length, breadth, and diameter); the camera has an adjustable spectrum that is perfectly suited for optical food sorting.
Machine vision algorithms and applications in beverage production
One of the most notable use cases of machine vision in food, or more specifically, beverage production, is Rockwell Automation's Pavillion8 analytics and machine vision system.
In short, it is a manufacturing production analytics application that can help beverage firms save time, eliminate errors, reduce energy use, improve quality, and increase efficiency. Using machine learning the program analyzes structured and unstructured data from multiple sources, such as devices, sensors, tags, and business systems relevant to manufacturing processes.
The system has been taught to recognize data points related to production, capacity, ingredients, energy usage, or machine status. The software can forecast ideal production capacity, ingredient quantities, energy consumption, and equipment maintenance dates. Rockwell Automation assisted Miraka, a dairy processing company, in implementing the Pavilion8 system in stages to optimize performance and profitability.
The first phase concentrated on evaporation processes, while the second phase used spray dryer model predictive control to increase output and capacity. The third phase concentrated on multivariable model predictive control to track liquid composition and standardize the process, resulting in better protein and fat content uniformity and less use of standardizing chemicals.
It makes sense to use custom computer vision software
Machine vision systems are an essential component of modern intelligent industrial systems. However, due to their complexity, existing vision systems are frequently modified and developed inefficiently. Generic closed-source machine vision development software is frequently underutilized. You may employ a professional computer vision model developer team to satisfy the vast demands of product appearance quality inspection in industrial production and increase the development efficiency and dependability of such systems.
Food production has the potential to be one of the industries that benefit the most from computer and machine vision. A software solution developed by a dedicated studio or team of developers supports manufacturers in automating processes, streamlining operations, and increasing production in multiple ways:
Vision-guided robots: Computer vision-powered robots can place products on the manufacturing line quickly and accurately, increasing production speed and precision.
Barcodes and text labels scanning: Because manual label scanning takes a significant amount of time and effort on the part of personnel, computer vision may be the missing link in efforts to automate and improve warehouse operations.
Defect reduction: Computer vision software can monitor the manufacturing line and guarantee that every manufactured item fulfills the approval standards considerably faster and more precisely than conventional staff.
Finding anomalies: Computer vision tools may assist in monitoring the manufacturing lines themselves, ensuring that no errors or harmful circumstances arise during the production process, in addition to monitoring the things that are being created.
Labeling, tracing, and tracking: Computer vision frameworks can assist in reducing expensive mislabeling and misplacing of merchandise.
Package inspection: Image processing tools assist businesses in maintaining product quality and ensuring that things meet needed packaging requirements, such as color or size.
While developing computer vision software in-house is certainly achievable (assuming you already have the necessary hardware), outsourcing this task to a professional will be significantly less expensive. Proficiency in the most widely used computer vision technologies, as well as experience with at least some additional tools and computer vision as a service solution, indicates a well-rounded computer vision developer who is likely to effectively implement your project.
Conclusion
The use of computer vision technology in food detection has substantially increased food inspection efficiency and supported the advancement of food safety, which is a key component of the intelligent process of food engineering. The application of computer vision systems allows for automated, objective, quick, and sanitary examination of a wide variety of raw and processed foods.
Machine vision has a high identification accuracy; nonetheless, there are detection mistakes in low light, high humidity, and high noise circumstances. As a result, high-resolution acquisition equipment must be developed to increase inspection quality and accuracy.
Although image processing is regarded as the heart of machine vision, a specific system needs to be tailor-made for most applications. At the same time, advanced processing software can enhance processing efficiency and recognition accuracy with the same received information. As a result, developing more efficient algorithms to make machine vision more acceptable for food inspection is even more critical than getting the right high-quality hardware parts.
Achieving accuracy is essential for machine vision systems, as incorrect readings can lead to the entire batch lot being recalled. To ensure the highest quality of production, developing the right software tools from a reputable developer is recommended. Contact us, and our team will be happy to help you and your manufacturing department develop a machine vision system to meet specific requirements.